1 Basic principles and structure of on-load tap-changer
An on-load tap changer is an electrical device that can change the tap position under excitation. The basic principle of voltage regulation by on-load industrial electrical tap changers is to lead out several taps in the transformer winding and use it to change the effective turns by switching from one tap to another without interrupting the load current. Number, that is, changing the voltage ratio of the transformer to achieve the purpose of voltage regulation. Therefore, during the operation of the on-load tap changer, firstly, the continuity of the load current must be ensured; secondly, it must have good arc breaking performance during the tap switching action.
During the tap change process of the on-load tap changer, a resistor must be used to realize the transition to limit the circulating current during the transition. Usually a resistive combination type on-load tap-changer is used. In actual work, the structure of the resistance current-limiting on-load tap-changer can be divided into three parts, namely, the switching switch, the selector switch, and the operating structure. Problems with any of these parts will directly affect the normal operation of the transformer.
2 Problems that occur during operation of the on-load tap-changer
2.1 Question 1
2.1.1 The contacts in the switch are hot
Frequent voltage regulation will cause serious mechanical wear, electrical corrosion and contact pollution between the contacts, especially for transformers with large load currents. The thermal effect of the current will weaken the elasticity of the springs, causing a gap between the moving and static contacts. The contact pressure decreases, the contact resistance increases, and the heat generation between the contacts increases. Heating accelerates oxidation corrosion and mechanical deformation of the contact surface, forming a vicious cycle, resulting in damage to the switch.
2.1.2 Preventive measures
Before maintenance and operation, the DC resistance of each tap position of the switch should be tested separately. During maintenance of the hanging hood, the contact resistance of the contacts should be measured to check whether the contact coating and contact are good. Each year, combined with maintenance or testing, rotate each gear position of the tap changer several times to remove the influence of oxide film or oil dirt and ensure good contact.
2.2 Question 2
2.2.1 Transition resistor disconnected and loose
If the transition resistor is disconnected or loose, the entire transformer will be burned down. If the transition resistor is switched with load when the transition resistor is burned out, not only will the load current be interrupted, but also the full phase voltage will appear on the transition resistor break and between the dynamic and static contacts. This voltage will not only break down the fracture of the resistor, but also generate a strong arc when the dynamic and static contacts are disconnected, resulting in a short circuit between the two transformer taps, causing the high-voltage winding tap section to be short-circuited and burned. At the same time, the arc rapidly decomposes the oil in the switch oil chamber and generates a large amount of gas. If the safety protection device cannot discharge these gases immediately, the switch will be damaged. The energy of the arc can also burn out the insulation barrel of the switch, rendering the switch irreparable.
2.2.2 Preventive measures
Strengthen the inspection of transition resistance.
⑴ Before the transformer leaves the factory, before operation and after overhaul, it is necessary to check whether the transition resistor is loosened and whether the resistance wire is mechanically damaged to avoid local overheating and burning during switching.
⑵For on-load switches that have switched more than 20,000 times or have been running for more than 2 years, it is necessary to check whether the material of the transition resistor has become brittle, whether the resistance has changed in value, and whether the fastening has become loose.
⑶ During operation, if the transformer is switched under a large current of more than 2 times the rated current, you must check whether the transition resistor is burned out.
⑷ There have been situations where the on-load switch does not switch, that is, the main spring of the rapid mechanism is fatigued or broken and does not work, the transmission system is damaged, the fasteners are loose, the machine is stuck, the limit failure, etc. make the switch unable to switch or the switch fails midway and the switching procedure When the time is extended beyond the specified value, it is necessary to check whether the transition resistor is burned out.
2.3 Question 3
2.3.1 Oil leakage from the oil chamber of the diverter switch
The diverter switch oil chamber is an independent oil tank. During operation, the oil in the oil chamber of the diverter switch is absolutely not allowed to enter the transformer body. This is because a certain arc is generated during operation of the diverter switch, which causes the quality of the oil in the oil chamber to deteriorate. This oil can only be stored in the oil chamber of the diverter switch. used in the transformer, but cannot enter the transformer body. Once it enters, it will seriously affect the chromatographic analysis of the oil inside the transformer, that is, the judgment of internal faults of the transformer. The causes of oil leakage in the diverter switch oil chamber are:
⑴The oil drain valve at the bottom of the on-load tap changer tank is not tightened, causing the oil in the transformer body tank to mix with the on-load tap changer tank.
⑵The sealing gasket between the two fuel tanks is made of poor material or the assembly process is poor. During on-site processing, it was found that most of the rubber pads did not work due to improper selection of the size of the rubber pads, and there was no margin after compression. In addition, the upper edge of the on-load tap changer tank is misaligned with the reserved hole in the main tank, making sealing more difficult. In some cases, the upper edge of the insulating cylinder of the on-load tap-changer oil tank is cracked, causing gaps, resulting in oil leakage.
⑶The oil seal of the central drive shaft is not tight.
2.3.2 Preventive measures
During operation, you should pay close attention to the oil level in the tap changer oil conservator. When the oil level in the oil conservator of the transformer rises or falls abnormally, you should check whether there is oil leakage in the diverter switch oil chamber. Take oil samples from the transformer regularly. If the chromatographic analysis of hydrogen, acetylene and total hydrogen content of the main transformer is found to be abnormally higher than the standard, you should also check whether there is oil leakage in the oil chamber of the diverter switch for timely processing.
2.4 Question 4
2.4.1 Deterioration of oil quality in on-load tap-changer
Every time the switch is operated, the insulation level of the switch decreases due to the deterioration of oil quality caused by arcing. Transformer oil is the most basic insulating material of tap changer. As an insulation and arc extinguishing medium, it also has cooling, lubrication and anti-corrosion functions. In the tap changer, due to the action of arc, the insulating oil in the switch oil chamber is decomposed, and free carbon, hydrogen, acetylene and other gases and grease are precipitated. The gas is generally discharged from the insulating oil, but free carbon particles and grease are Part of it is mixed in the insulating oil, and part of it accumulates on the surface of the insulating parts of the switch. In addition, a small amount of metal particles sputtered out after the contact material melted also remained on the surface of the insulator. The increase of these deposits will increase the leakage current, reduce the insulation resistance, and eventually cause the oil to discharge along the insulation surface, causing the switch to be damaged.
2.4.2 Preventive measures
After running for 6-12 months or switching 2000-4000 times, the oil sample in the switch box should be taken for testing. After switching 5,000 to 10,000 times or when the breakdown voltage of the insulating oil is lower than 25kV, the insulating oil in the switch box should be replaced and the surface of the insulating parts should be cleaned.
XZTZ5001 Transformer Core Grounding Current Tester
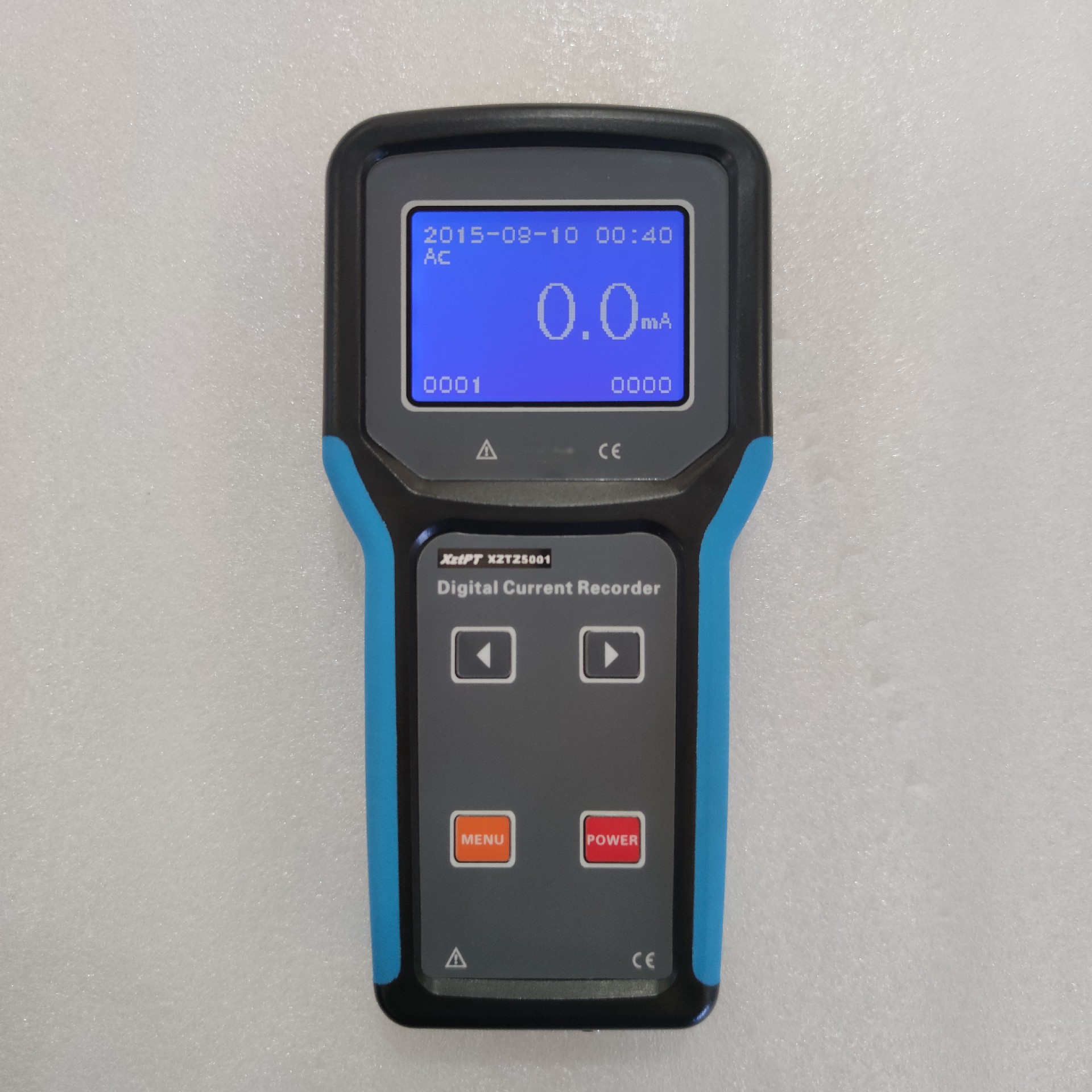