Transformers are one of the key electrical equipment in power distribution stations. Oil-immersed transformers are widely used because they have good dielectric strength, strong heat transfer performance and low construction costs. They can solve the problem of heat pipe heat dissipation in large spaces and the problem of high working voltage insulation layers in transformers. use. However, oil leakage is a common problem in the operation of oil-immersed transformers, which seriously affects the safe operation of the transformer.
Transformer oil leakage will pose a serious threat to the safe operation of the transformer. First, if the transformer leaks oil for a long time or has a large amount of oil leakage, there will be insufficient aviation hydraulic oil. When the aviation hydraulic oil level during operation drops too much, it may cause coal bed methane maintenance malfunction. When the transformer is seriously short of oil and the internal windings are exposed, it may cause damage to the insulation layer and even cause a thermal breakdown accident, causing the transformer to shut down and affecting the reliable supply of power projects. Second, oil leakage from the transformer can easily lead to Moisture enters, causing moisture to return to the inside of the transformer; third, the leaking oil location of the transformer is easy to adhere to dust, causing large-scale oil stains to adhere to the surface, which greatly affects the appearance and image, making maintenance difficult; fourth, aviation hydraulic oil leaks Waste of water resources and environmental pollution. Therefore, the problem of transformer oil leakage must attract the attention of substation maintenance personnel.
Analysis of causes of transformer oil leakage
There are many reasons for transformer oil leakage, which are often related to the manufacturing quality of parts, software environment, installation quality, operation period, etc. To summarize the reasons for transformer oil leakage in recent years, the main aspects are as follows.
1. The sealing gasket is brittle
Transformer oil leakage mostly occurs at the connection between the fuel tank and spare parts, and about 90% is mainly caused by the aging of the sealing gasket. The key to the quality of sealant parts lies in its wear resistance. If the wear resistance is weak, the embrittlement rate will be rapid, especially at high temperatures. The temperature of the transformer during operation reaches about 70 ℃. It is very easy to cause the hydraulic seal to become brittle, deformed, and even ineffective, causing oil leakage in the transformer.
2. Operating in a difficult environment
Most transformers operate outdoors, operating in harsh environments with large temperature differences. The average outdoor temperature reaches 42°C in summer and subzero 15°C in winter. Coupled with the heat generated during the operation of the transformer itself, long-term thermal expansion and contraction cause the sealing gasket to lose its ductility, causing oil leakage.
3. Poor welding quality
The oil-immersed transformer is a combination of various welding and connections based on a thick steel plate welding casing. During production, the fuel tank has many spot welds, long welds, and difficult welding. Welding materials, welding methods, welding The technical strength of the welding staff will affect the quality of electric welding. For example, each 31,500 kVA transformer has more than 70 spot welds. Welding holes, sand holes, weak welds, poor contacts and other shortcomings cause oil leakage in the transformer.
4. Mechanical processing technology
The machining process and procedures do not meet the regulations. The tightening is too loose or too tight during the assembly line. The sealing gasket is not cleaned or is uneven. The flange of the looper of each component is uneven. Human factors during installation cause the footing around the sealing gasket. The bolts are not uniformly supported; the flange connection head is deformed and displaced. This situation often occurs at the relay of the coal bed methane vehicle and the connection between the radiator and itself. There are also cases where the waterproof casing of large transformers is poorly installed and supported at the joints of the waterproof casing, which can easily cause oil leakage at the waterproof casing.
5. The harm of maintenance staff’s technical strength
At present, the company's frontline maintenance team has a serious problem of staff breakage. Due to the limitations of staff and machinery, transformer maintenance mostly relies on outsourced teams. The outsourced staff had a weak sense of responsibility, did not strictly implement technical specifications during maintenance, did not carefully search for the cause of leakage, did not test for leakage after repair, or did not have enough negative pressure time, resulting in defects still existing after repair.
6. Destruction by external force
When the transformer is being transported and lifted, the parts are impacted, the hoses such as the radiator are distorted by external forces, or other components are injured and deformed, the welding joints are opened, cracks and other hidden defects occur. After the transformer is put into operation, the temperature rises. The working pressure increases, causing oil leakage.
How to deal with transformer oil leakage
Before dealing with oil leakage, careful analysis must be carried out to find out the cause of the leakage and the exact leakage point. For existing oil stains, first clean them with a small flat shovel and wire brush, then clean them with cleaning agents such as perchlorethylene, acetone, alcohol, etc., rinse them with clean water, and finally wipe them repeatedly with a clean cloth to find the exact location of the leakage point. .
1. Use welding to control transformer oil leakage
When oil leakage is found in the upper part of the transformer oil tank, only a small amount of oil needs to be discharged before welding treatment; when leakage is found in the lower part of the oil tank, since the draining of oil from the hanging core is too wasteful and subject to site conditions, welding with oil can be used. Repair welding with oil should be carried out under the condition that the oil leakage is not obvious. Otherwise, the vacuum oil draining method should be used to create negative pressure before welding. The degree of vacuum of the negative pressure should not be too high. It is appropriate to make the internal and external pressures equal to avoid inhalation of molten iron. When repairing welding, the oil traces on the welding parts should be removed. It is best to rinse them with alkaline water and then wipe them dry. During the welding process, attention should be paid to preventing penetration and fire. The welding parts must be below the oil level. Use breakage during welding. Continued, for fast spot welding, the arcing time should be controlled within 10s to 20s, and long-term continuous welding is absolutely not allowed. When repairing welding pores with serious oil leakage, you can first plug or rivet with iron wires, etc. before welding; when welding near sealing rubber gaskets or other vulnerable parts, cooling and protection measures should be taken.
2. On-site fast bonding method to seal oil leakage from transformer
Sole carbon nanopolymer material is a cold welding bonding technology. Its advantages are strong bonding force, strong weather resistance, and comprehensive mechanical properties such as elastic deformation of metal. It can achieve online control of transformer oil leakage while ensuring safety.
XZT 7111 High Voltage Circuit Breaker Tester
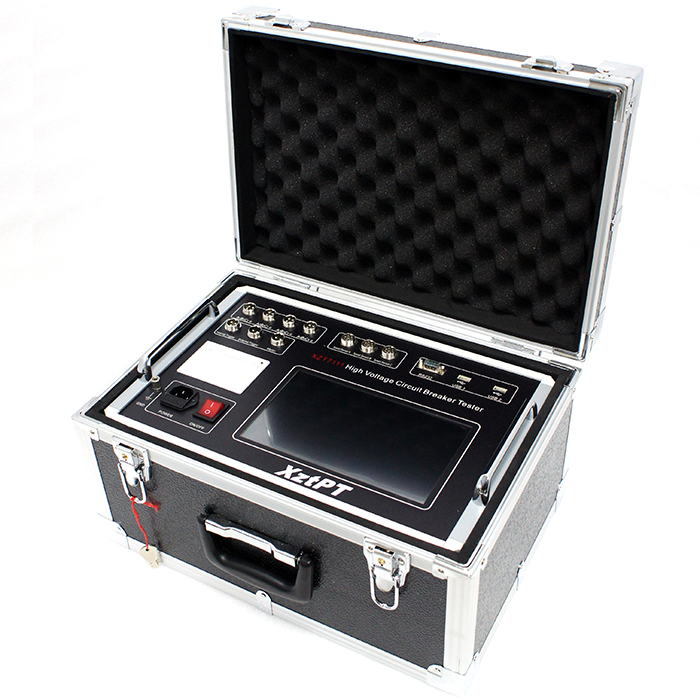